Selecting the right industrial conveyor rollers is critical to ensuring your system operates efficiently, reliably, and with minimal downtime. Whether you’re in mining, logistics, packaging, or food processing, choosing the proper roller type can make a big difference in productivity and maintenance costs.
Below, we’ll walk you through the key factors in conveyor roller selection to help you make informed decisions.
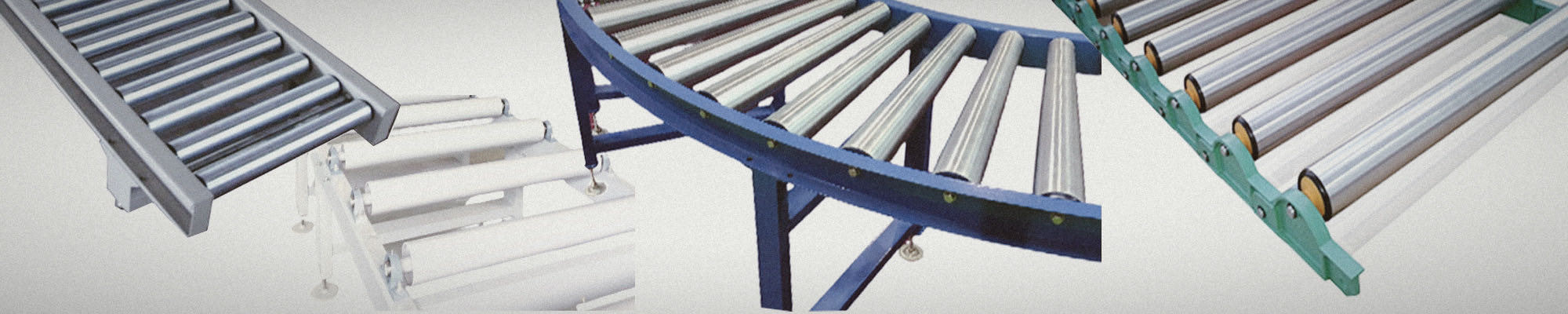
Suitable Industries and Applications
Different industries require different types of rollers based on load, environment, and material handling needs:
■ Mining & Quarrying: Requires heavy-duty steel rollers with high load capacity and wear resistance. Sealed bearings help protect against dust and debris.
■ Logistics & Warehousing: Usually use light- to medium-duty rollers. These can be made of plastic or zinc-coated steel. They are used for handling parcels and sorting lines.
■ Packaging & Distribution: Grooved or spring-loaded rollers support automated conveyor systems where precision and quick replacement are important.
■ Food Processing: Stainless steel rollers are preferred for their corrosion resistance and hygienic surface, suitable for washdown environments.
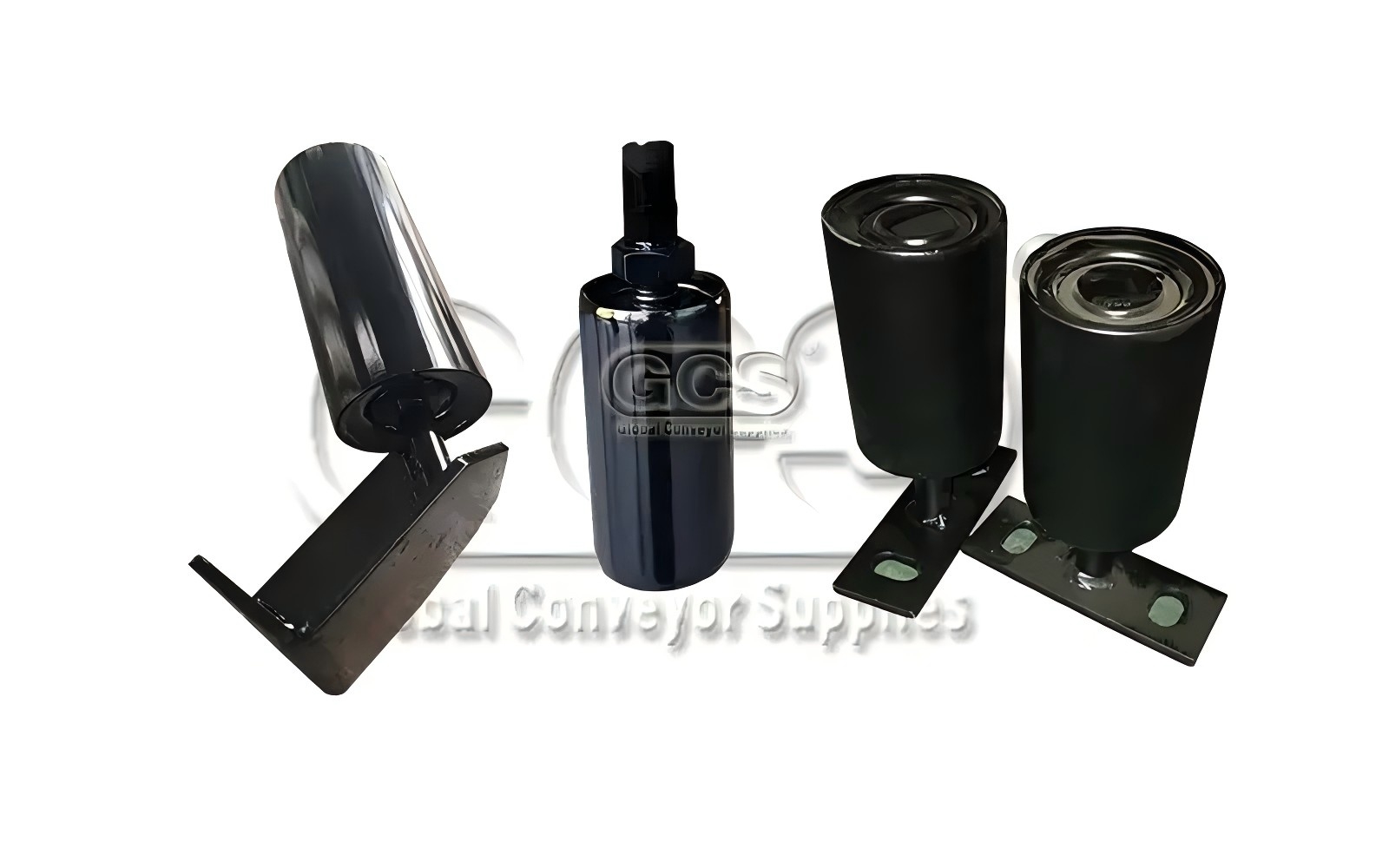
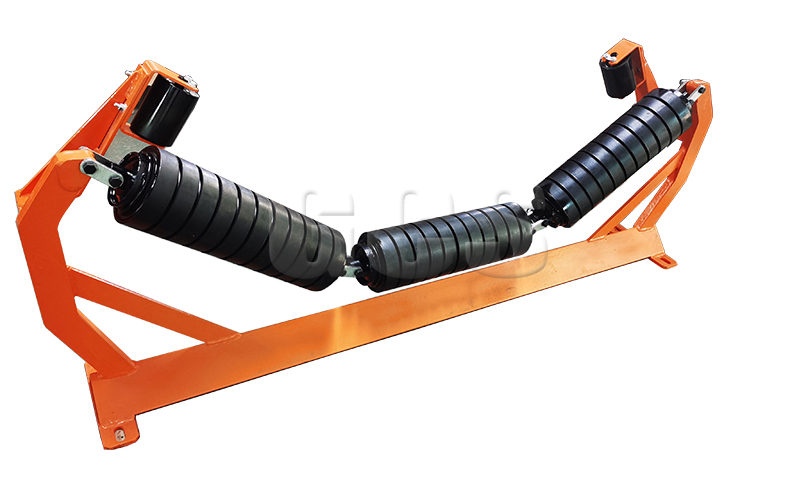
Key Technical Parameters to Consider
Choosing the right roller involves balancing performance, durability, and compatibility. Focus on the following:
1. Material
● Steel: High strength, ideal for heavy-duty and high-temperature environments.
● Plastic/Polymer: Lightweight, corrosion-resistant, quieter operation.
● Stainless Steel: Food-grade and chemical-resistant.
2. Load Capacity
● Know your system’s max load per roller.
● Consider dynamic vs static loading.
● For heavy loads, thicker tubing and reinforced shafts are necessary.
3. Shaft Type & End Design
● Options include spring-loaded, fixed, female threaded, and hexagonal shafts.
● Shaft type affects ease of installation, especially for tight conveyor frames.
4. Surface Treatment
● Zinc plating or powder coating for rust resistance.
● Rubber lagging or PU coating for improved grip or shock absorption.
● Smooth vs knurled finish, depending on conveyed material.
Types of Conveyor Rollers We Offer
Type | Description | Suitable For |
---|---|---|
Gravity Rollers | Unpowered rollers for manual or slope-fed systems. | Warehousing, assembly lines |
Grooved Rollers | With grooves for O-belt or V-belt drive. | Driven systems, sorters |
Spring-Loaded Rollers | Easy to install; compressible ends. | Light-duty conveyors |
Motorized Drive Rollers (MDR) | Integrated motor inside the roller. | Smart logistics, e-commerce |
Plastic Conveyor Rollers | Lightweight and quiet. | Food, electronics, clean rooms |
Common Mistakes & Expert Tips
Avoid these pitfalls when selecting conveyor rollers:
■ Ignoring environmental conditions — Heat, moisture, and chemicals can degrade standard rollers quickly. Always choose materials that match your operating environment.
■ Overlooking system speed and spacing — Rollers must match your conveyor’s speed and support intervals. Faster systems need more precise and balanced rollers.
■ One-size-fits-all approach — Conveyor roller types vary widely. Don't use the same roller design across different production lines without verification.
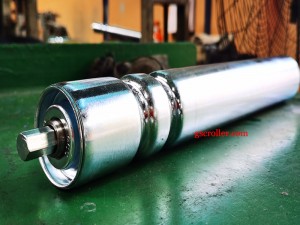

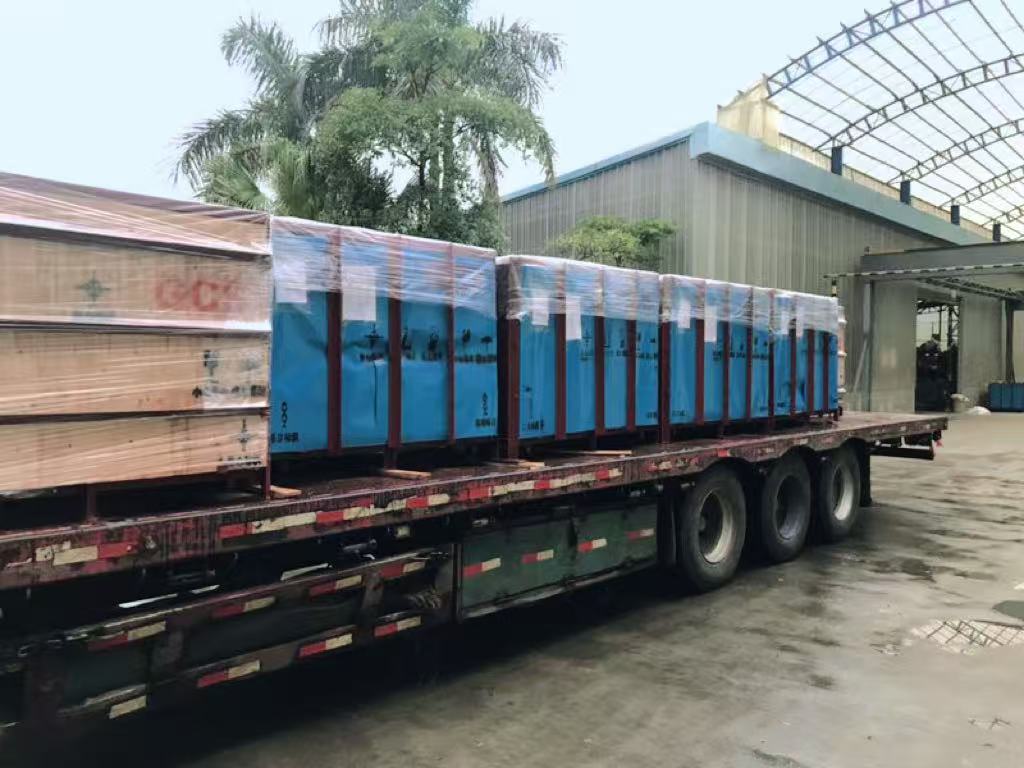
Need help with industrial conveyor roller selection?
Contact our engineering team for tailored advice and a quote on standard or customized rollers for your application. For more product information, please click here.
Post time: Jul-15-2025