Characteristics and advantages of ultra-high molecular weight polyethylene rollers
The roller is an important component and vulnerable part of the conveying equipment, and its quality directly determines the service life of the conveying equipment and how much power it consumes. The conveying equipment rollers currently in use in our country mostly use metal rollers. Compared with the rollers of similar foreign products, there are shortcomings such as short service life, large operating resistance coefficient, and large weight of the rollers. Moreover, general metal roller products are only suitable for general production occasions. In mines with higher requirements for noise and static electricity, corrosive coking plants, chemical companies, and other special occupations, the length of application is 6 months, short One month has brought great restrictions and risks to the production of conveying equipment. Safety accidents have occurred repeatedly, resulting in large losses and high energy consumption. In view of the huge amount of rollers used and the huge power consumption, the transformation of traditional metal rollers burned the eyebrows. Based on this, we developed ultra-high molecular weight polyethylene rollers based on the status quo of domestic and foreign skills, on the basis of general metal rollers, and through innovations in skills, structure, and process equipment.
1. Roller of UHMWPE data
Polyethylene with a molecular weight of more than 1.5 million is called “UHMW-PE”, which is used as an engineering plastic because of its excellent physical functions. When we select raw materials, we first consider the following excellent application functions:
(1) Wear resistance The wear resistance of UHMWPE ranks first among plastics and surpasses certain metals. Such high wear resistance makes it difficult to test its wear resistance by general plastic wear test methods. Therefore, mortar wear is selected. In test equipment, wear resistance is proportional to molecular weight, as the molecular weight increases, the wear resistance will be better;
(2) Impact resistance and impact energy absorption. It is difficult to break and damage by general impact test methods. Its impact strength increases with the increase of molecular weight, reaching the maximum when the molecular weight is 1.5 million, and then continues to increase with the molecular weight. And gradually decline. In addition, it has a higher surface hardness after repeated impact; it has excellent impact energy absorption, which has the highest impact energy absorption value among all plastic models, so it has good noise damping and excellent noise reduction;
(3) Self-lubricating UHMWPE has a very low conflict factor (0.05~0.11), so it is excellent in self-lubricating. From Table 1, it can be seen that the conflict factor is inferior to the best self-lubricating polytetrafluoroethylene ( PTEE), so it is hailed in the field of conflict science as a material with ideal capital functions;
(4) Chemical resistance. It has excellent chemical resistance. In addition to strong oxidizing acids, it can withstand various corrosive media (such as acids, alkalis, and salts) and organic media at a certain temperature and depth. The tea solvent is outside). It is immersed in 80 kinds of organic solvents at 20°C and 80°C for 30 days without any abnormal appearance, and other physical functions are almost unchanged;
(5) Non-stick UHMWPE has a very weak surface adsorption force, and its anti-adhesion ability is second only to PTEE, which is the most non-sticky in plastic, so the appearance of the product is not easy to adhere to other materials. In addition, UHMWPE also has the characteristics of low-temperature resistance (making the roller applicable to a large scale), hygienic, non-toxic, and hydrophobic (the roller is not easy to absorb water and deform).
The shortcomings of UHMWPE: Compared with metals and other engineering plastics, the heat resistance, and hardness are lower, but they can be improved by “filling” and “crosslinking”.
2. The superiority of ultra-high molecular weight polyethylene conveyor idler roller
(1) Because the operating resistance coefficient and rolling inertia are greatly reduced, the roller operation becomes more sensitive and stable. Ultra-high molecular weight polyethylene has a good impact on energy absorption and damping, which can effectively reduce the operating noise and enable the conveying equipment to complete Long haul distance, large capacity, and high-speed operations. However, considering the shortcomings of the low strength of polyethylene raw materials, it is necessary to pass steady calculations and experiments.
(2) Because the ultra-high molecular weight polyethylene roller has the appearance of non-sticking, non-rusting, and self-lubricating, it has better protection for transportation, even when the roller is damaged and does not roll, it will not be damaged. The conveyor belt is not easy to wear and the service life of the conveyor belt, conveyor roller
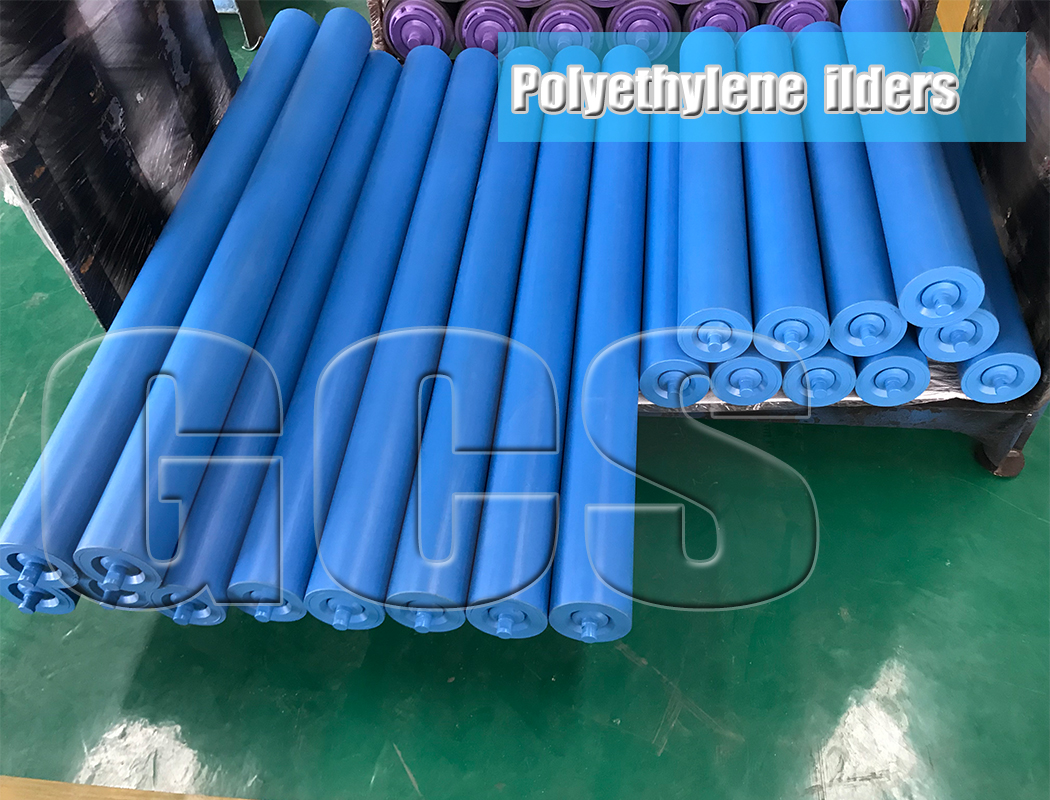
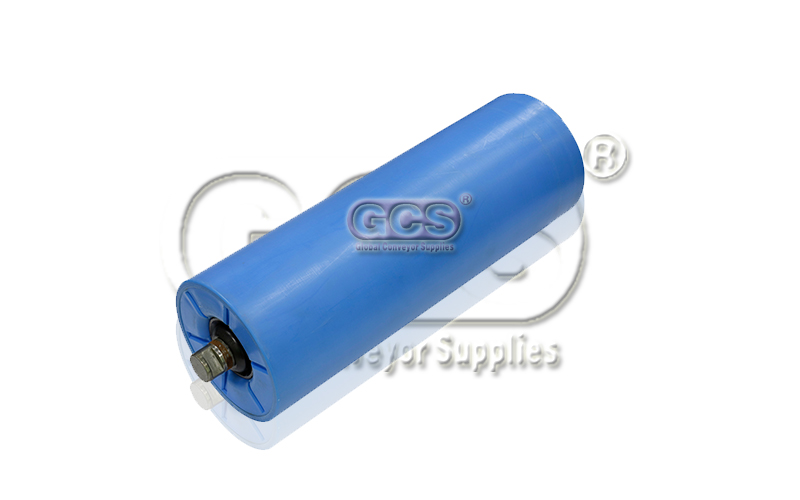
The UHMWPE Plastic Conveyor Belt Roller retains all the excellent properties of ultra-high molecular weight polyethylene, with anti-friction self-lubrication, impact resistance, noise and vibration elimination, anti-adhesion, anti-corrosion, anti-aging, and so on. After being put on the market, the UHMWPE Plastic Conveyor Belt Roller has withstood the test of long-term use and has been well received by customers. It is widely used in metallurgical mines, coal mines, chemical industry, grain storage, building materials, ports, salt fields, electric power, and other industries. The best alternative.
Since most of the rollers are exposed to dust and water pollution, and the material is worn or corroded by the roller body, the ideal roller must have three core technologies:
1. The labyrinth seal that never contaminates. Technology;
2. roller manufacturing precision, consistency of technology;
3. roller body anti-corrosion and wear-resistant technology.
Feature
Can control the bearing life cycle, planned predictive maintenance;
Solving the contradiction that the traditional roller sealing performance is good and the rotation resistance is correspondingly large;
Extend the life of the tape, roller rubber surface, reducer, and motor by more than 5 times;
Exempting a large amount of manpower and material resources for maintenance;
Significantly reduce the labor intensity of workers and improve their health;
The different environments can choose different materials of the roller, the most reasonable investment, and operating costs;
Reduce downtime, improve the overall economic benefits of transportation 5-8 times.
Effective sealing system
The primary labyrinth seal prevents most of the dust to get into the bearing house, and no water could leak in. The narrow
clearance between bearing house and shaft forms the second sealing, the bearing house are made of UHMWPE which has a
very low surface energy and are anti-adhesion, so it is repulsive to dust and water. It is quite difficult for the dust to get through the
narrow channel
HDPE roller
UHMWPE HDPE Material Conveyor Rollers
Custom polyurethane idler rollers
Post time: Aug-10-2021