Composite Conveyor Rollers Manufacturer
Bulk & Custom Solutions from China
We are a professional composite conveyor roller manufacturer located in China, specializing in bulk supply and OEM/ODM customization.
Our rollers are designed for mining, bulk material handling, and industrial conveyor systems. They offer high impact resistance, a lightweight structure, and a long service life.
We provide strong and affordable composite roller solutions. This is true whether you are a conveyor system integrator, a distributor, or a plant owner. We deliver these solutions worldwide.
Partner with us for high-performance composite conveyor rollers.
Customization – Tailored to Your Conveyor System
Conveyor rollers made with a tube of composite materials are called composite rollers or composite idler rolls.
Dimensions & Load Rating
Diameter: 89mm, 102mm, 127mm, 152mm, or custom sizes
Shaft: Hexagonal, round, or keyed; stainless steel or galvanized
Load capacity customized per application
Material Selection
Outer shell: HDPE, UHMWPE, nylon, PU
Bearing housing: Steel, nylon, or zinc-coated
Shaft seal options: Contact/labyrinth/sealed-for-life
Branding & Packaging
Custom logo on roller ends or shafts
Palletized export packaging with labels
Technical drawing or engineering support for system integration
Product Showcase – Composite Conveyor Roller Types
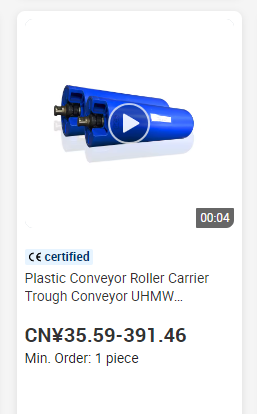
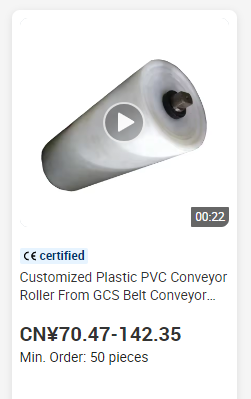
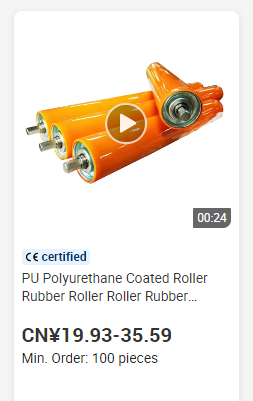
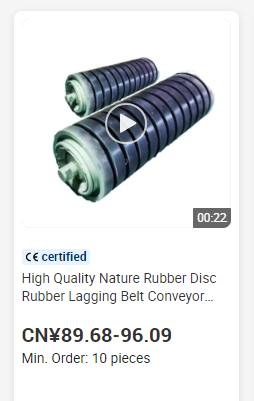
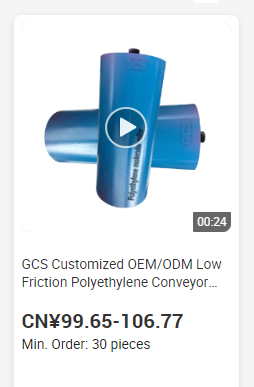
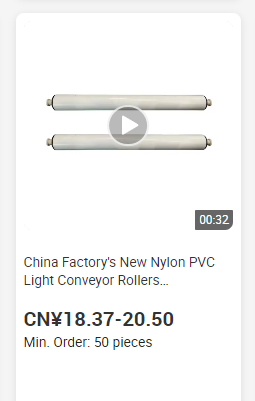
Why Choose Composite Conveyor Rollers from Our Factory?
Advanced Composite Material Technology
Outer shell: High-density polyethylene (HDPE), PU.
Inner core: Precision-balanced steel/aluminum tubing
Bearings: Sealed deep-groove ball bearings with labyrinth protection
Superior Mechanical Performance
Lower noise and friction coefficient than traditional steel rollers
Water-proof, anti-static, and non-corrosive
High strength-to-weight ratio, reduces belt wear
Ideal for Harsh Environments
Mines, ports, cement, coal, fertilizer plants
Resistant to chemicals, saltwater, moisture, and high impact
Longer lifespan than traditional steel rollers under the same conditions
Reduce weight, cut costs—choose composite conveyor rollers now!
Quality Assurance and Certifications
Whether you're in mining, port logistics, or industrial automation, GCS delivers reliable components that keep your systems running smoothly.
■ ISO-certified manufacturing standards
■ Quick turnaround times and global delivery
■ Responsive engineering support
■ Proven reliability in over 40 countries
Let's upgrade your system with durable composite conveyor rollers today.
Global Projects & Export Capacity
Trusted by conveyor OEMs and system integrators in over 30 countries, including Australia, South Africa, Chile, UAE, and Canada.
■ Export experience with CE / ISO / SGS certifications.
■ 10,000㎡ facility with a monthly output of 50,000+ rollers.
■ Fast lead time: 15–20 days for bulk orders.
■ Custom solutions for mining, cement, steel, and agricultural industries.
Ordering Process – From Inquiry to Delivery
A smooth and professional process for global B2B buyers:
Send your specifications – Drawings or application details
We provide quotation & technical drawing – Fast response within 24h
Sample testing – Optional prototype support
Mass production – QC, packaging, and delivery support
After-sales support – Continuous technical assistance
Contact our team today to receive a free quote or schedule a technical consultation.
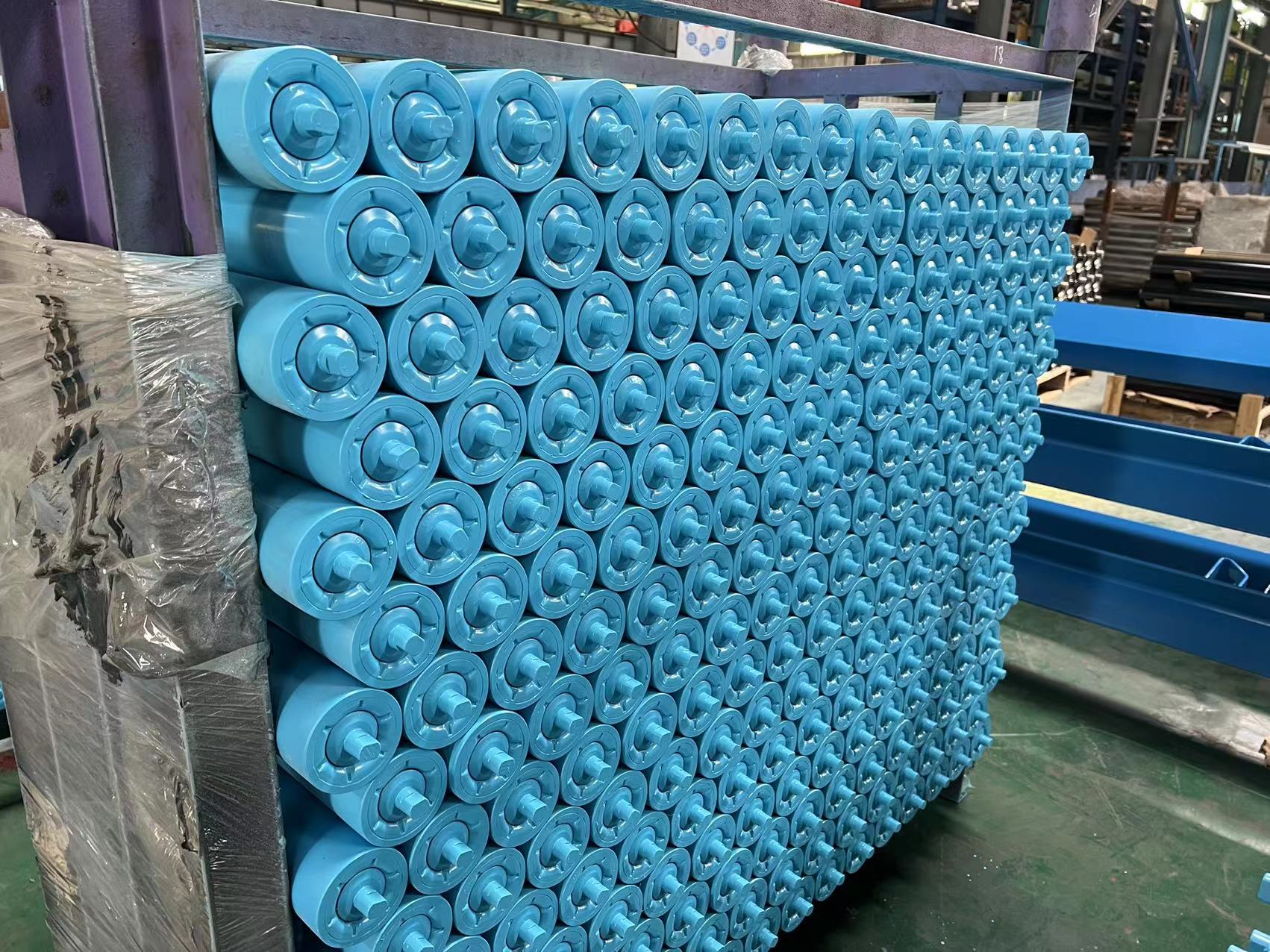
Other Composite Conveyor Rollers You Might Like
Technical Guide & Expert Insights
1. Composite vs. Traditional Metal Conveyor Rollers – A Performance Comparison
√ Lightweight Efficiency: Composite rollers are 30%–50% lighter than steel rollers, significantly reducing energy consumption across conveyor systems.
√ Corrosion Resistant: Made with HDPE, UHMWPE, or fiberglass shells, composite rollers won’t rust, making them ideal for wet, acidic, or alkaline environments such as mining, fertilizer handling, and seaports.
√ Low Noise Operation: Composite rollers generate less operational noise than metal ones — a critical benefit for noise-sensitive or environmentally regulated facilities.
√ Reduced Belt Wear: Smooth surface materials lower friction with the conveyor belt, extending belt lifespan and reducing maintenance costs.
√ Long Service Life: With excellent impact resistance, anti-aging properties, and low-temperature durability, composite rollers perform reliably in harsh and demanding conditions.
For more details, you may see here.
2. Structural Breakdown of a High-Performance Composite Conveyor Roller
Understanding the internal components of a composite roller helps buyers assess product quality:
● Shell Material: HDPE / UHMWPE / Nylon / PU
Provides corrosion resistance and impact protection.
● Inner Tube: Galvanized steel / Aluminum alloy / High-strength fiberglass
Delivers core strength and rigidity.
● End Caps: Injection-molded nylon or steel
Secure the bearings and connect the roller body.
● Bearings: Precision deep-groove ball bearings (typically sealed type)
Ensure smooth rotation, low friction, and long service life.
● Sealing System: Labyrinth seals + oil seals
Keep out dust, moisture, and contaminants to extend product lifespan.
3. Recommended Composite Conveyor Roller Types by Application Scenario
Different working environments require different roller types. Here's a practical guide:
■ Standard Carrying Rollers
For general conveyor sections — lightweight, economical, and durable.
Installed at loading points — with rubber rings to absorb material impact.
For the return side of the belt — available with optional cleaning features.
■ Friction / Self-Cleaning Rollers
For sticky materials like coal slurry or lime powder, it prevents material build-up.
■ Anti-Static Rollers
Used in fire-hazard or static-sensitive environments such as grain silos and chemical plants.
4. Composite Conveyor Roller Selection Guide (Matching Technical Parameters)
Parameter | Details |
---|---|
Outer Diameter | Standard sizes: Φ89, 102, 127, 152mm; custom sizes available |
Roller Length | Customized according to belt width (e.g., B500, B650, B800) |
Shaft Size & Type | Common diameters: 20/25/30/35mm; options include round, keyed, hex shafts |
Operating Temperature | Standard range: -40°C to +80°C; low-temp resistant materials available |
Mounting Options | Bracket hole distances and connection types tailored to site specifications |