Amongst all types of roller idler conveying equipment, roller conveyors have an extremely wide range of applications and a sturdy position that cannot be ignored. Roller conveyors are used in courier, postal service, e-commerce, airports, food and beverage, fashion, automotive, ports, coal, building materials, and various other manufacturing industries.
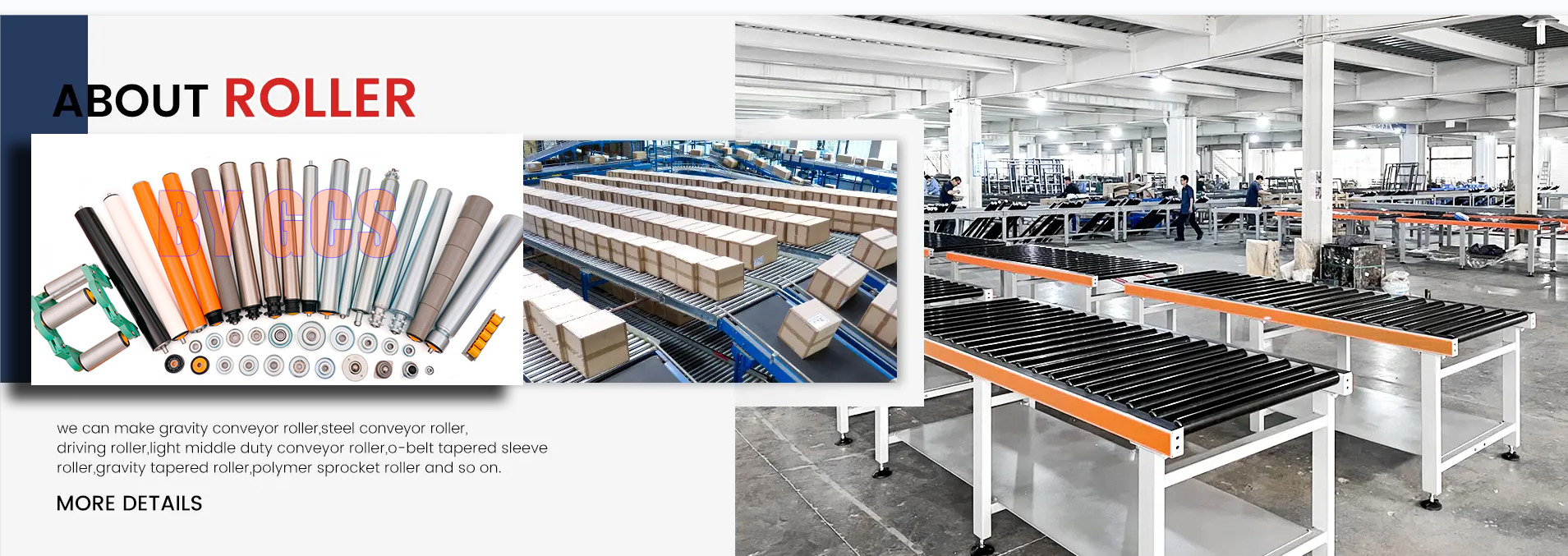
Goods suitable for roller conveyors should have a flat, rigid contact bottom surface, e.g. rigid cardboard boxes, flat-bottomed plastic boxes, metal (steel) bins, wooden pallets, etc. When the contact surface of the goods is soft or irregular (e.g. soft bags, handbags, parts with irregular bottom, etc.), they are not suitable for roller conveying. It should also be noted that if the contact surface between the goods and the roller is too small (point contact or line contact), even if the goods can be conveyed, the roller will be easily damaged (partial wear, broken cone sleeve, etc.) and the service life of the equipment will be affected, e.g. metal bins with mesh bottom contact surface.
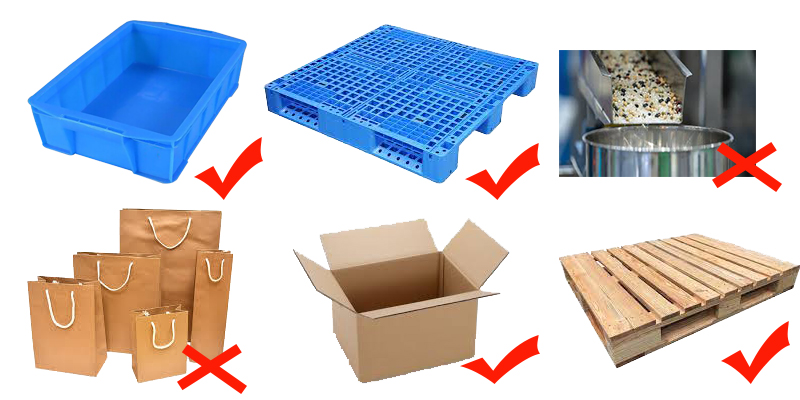
Selection of roller type
When using manual pushing or inclined free sliding choose a non-powered roller; when using an AC motor drive choose a power conveyor roller, power conveyor rollers can be divided into single sprocket drive rollers, double sprocket drive rollers, synchronous belt drive rollers, multi vertically belt drive rollers, O belt drive rollers, etc. depending on the drive mode; when using an electric roller drive choose an electric roller and a power roller or a non-powered roller When goods are required to stop accumulating on the conveyor line, the accumulation pulley can be selected, depending on the actual accumulation needs of the sleeve accumulation (friction is not adjustable) and adjustable accumulation pulley; when the goods need to achieve turning action to choose a conical roller, different manufacturers standard conical roller taper is generally 3.6 ° or 2.4 °, with 3.6 ° most often.
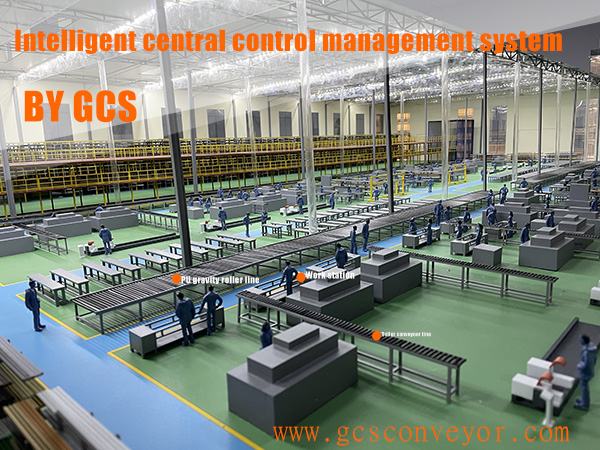
Selection of roller material:
Different use environment needs to choose different materials of roller: plastic parts in low-temperature environment brittle, not suitable for long time use, so low-temperature environment needs to choose steel roller; The roller will produce a small amount of dust when used, so it can not be used in a dust-free environment; Polyurethane is easy to absorb external colors, so it can not be used to transport cartons and goods with printing colors; Stainless steel drum should be selected in the corrosive environment; When the conveying object will cause greater wear on the roller, the stainless steel or hard chrome plated roller should be selected as far as possible because of the poor wear resistance of the galvanized roller and the poor appearance after wear. Because of the need for speed, climbing, and other reasons, the rubber drum is used, the rubber drum can protect the goods on the ground, reduce the transmission noise, and so on.
Selection of roller width:
For straight line conveying, under normal circumstances, the length of the drum W is 50~150mm wider than the width of the goods B. When the positioning is required, it can be selected as small as 10~20mm. For goods with great rigidity at the bottom, the width of the goods can be slightly greater than the length of the roll surface without affecting normal transportation and safety, generally W≥0.8B.
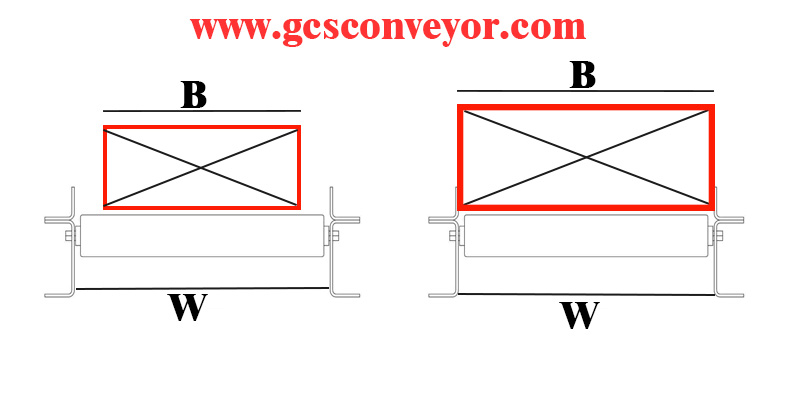
For the turning section, it is not only the width of the goods B that affects the roller length W. Both the length of the goods L and the turning radius R have an influence on it. This can be calculated from the formula in the diagram below, or by turning the rectangular conveyor L*B around the center point as shown in the diagram below, ensuring that the conveyor does not rub the inner and outer guide edges of the conveyor line and that there is a certain margin. The final adjustment is then made according to the roller standards of the different manufacturers.
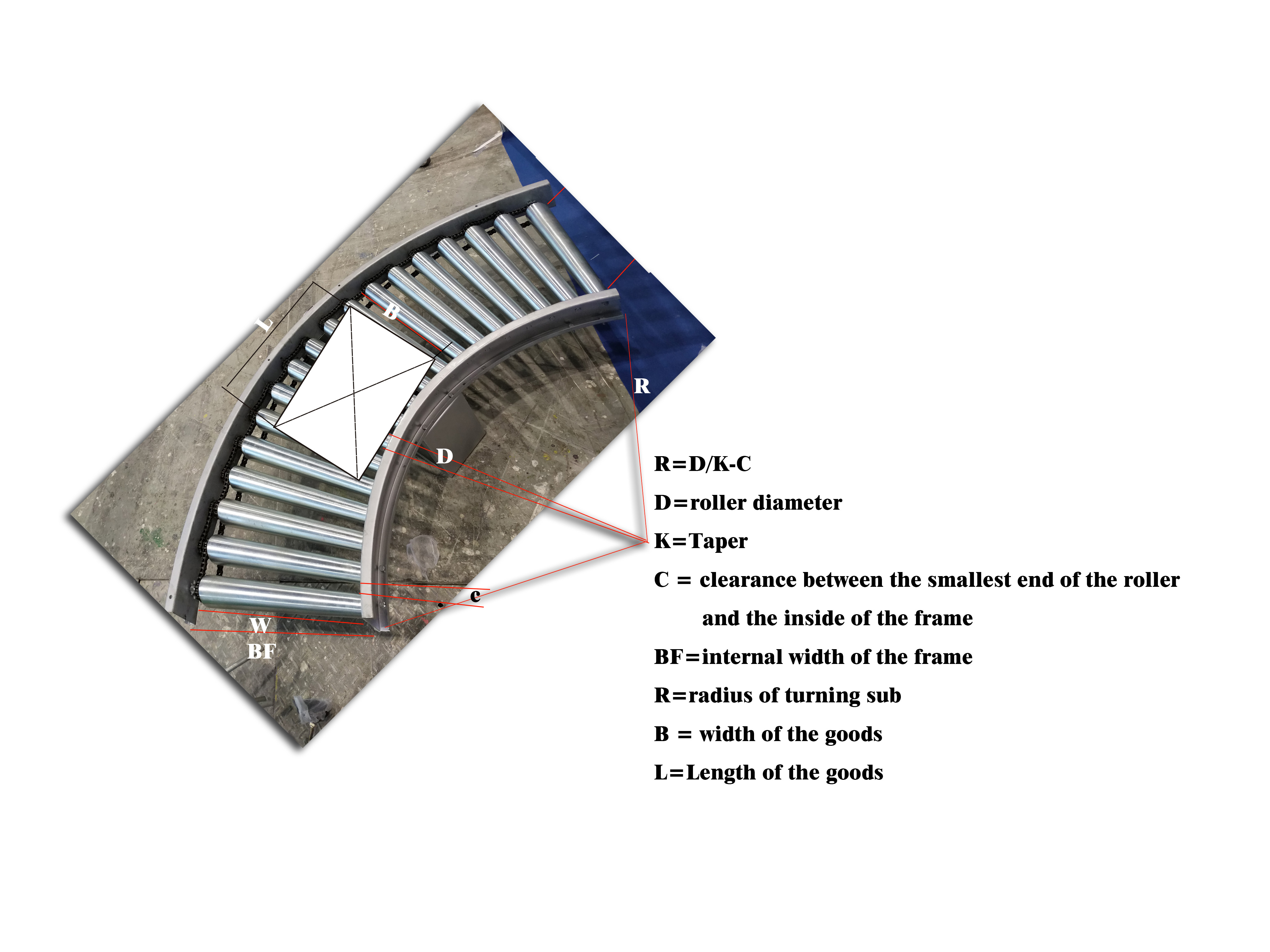
With the same width of goods in both the straight section and turning section of the line body, the length of the roller required by the turning section will be greater than the straight section, generally take the turning section as the uniform length of the roller conveying line, such as inconvenient to unify, can set the transition straight section.
Selection of roller spacing.
To ensure the smooth transport of goods, at least 3 or more rollers should support the goods at any given moment, i.e. the roller center spacing T ≤ 1/3 L, generally taken as (1/4 to 1/5) L in practical experience. for flexible and slender goods, the deflection of the goods also needs to be considered: the deflection of the goods on a roller spacing should be less than 1/500 of the roller spacing, otherwise, it will greatly increase the running resistance. It also needs to be confirmed that each roller cannot carry more than its maximum static load (this load is the evenly distributed load without shocks, if there is a concentrated load, a safety factor also needs to be increased)
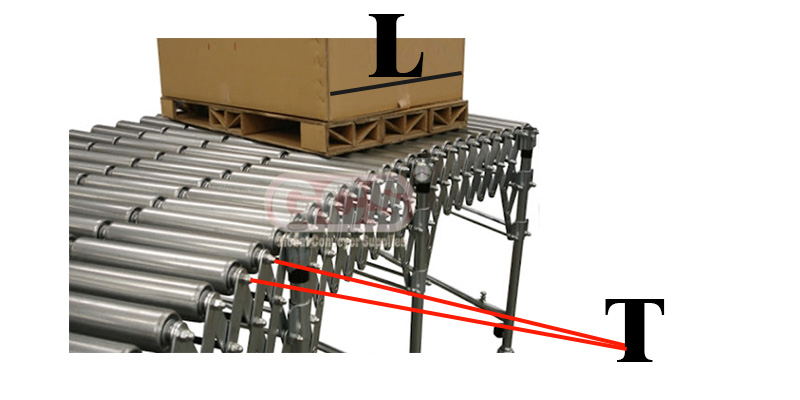
In addition to meeting the above basic requirements, the roller pitch also needs to meet some other special requirements.
(1) Double chain drive roller center distance should comply with the formula: center distance T=n*p/2, where n is an integer, p is the chain pitch, in order to avoid chain half buckle, the common center distance is as follows.
Model | Pitch(mm) | Recommended center distance(mm) | Tolerance(mm) | ||||
08B11T | 12.7 | 69.8 | 82.5 | 95.2 | 107.9 | 120.6 | 0/-0.4 |
08B14T | 12.7 | 88.9 | 101.6 | 114.3 | 127 | 139.7 | 0/-0.4 |
10A13T | 15.875 | 119 | 134.9 | 150.8 | 166.6 | 182.5 | 0/-0.4 |
10B15T | 15.875 | 134.9 | 150.8 | 166.6 | 182.5 | -198.4 | 0/-0.7 |
2)The center distance of the synchronous belt arrangement has a relatively strict limit, the common spacing and the matching synchronous belt type are as follows (recommended tolerance: +0.5/0mm)
Timing belt width:10mm | ||
Roller pitch(mm) | Model of timing belt | Teeth of timing belt |
60 | 10-T5-250 | 50 |
75 | 10-T5-280 | 56 |
85 | 10-T5-300 | 60 |
100 | 10-T5-330 | 66 |
105 | 10-T5-340 | 68 |
135 | 10-T5-400 | 80 |
145 | 10-T5-420 | 84 |
160 | 10-T5-450 | 90 |
3) The pitch of the rollers in a multi-V belt drive should be selected from the following table.
Roller pitch(mm) | Types of poly-vee belt | |
2 Grooves | 3 Grooves | |
60-63 | 2PJ256 | 3PJ256 |
73-75 | 2PJ286 | 3PJ286 |
76-78 | 2PJ290 | 3PJ290 |
87-91 | 2PJ314 | 3PJ314 |
97-101 | 2PJ336 | 3PJ336 |
103-107 | 2PJ346 | 3PJ346 |
119-121 | 2PJ376 | 3PJ376 |
129-134 | 2PJ416 | 3PJ416 |
142-147 | 2PJ435 | 3PJ435 |
157-161 | 2PJ456 | 3PJ456 |
4) When driving an O belt, different preload should be selected according to the suggestions of different O belt manufacturers, generally 5%~8% (that is, 5%~8% is deducted from the theoretical bottom diameter ring length as preload length)
5) When using the turning drum, it is recommended that the included Angle of drum spacing for double chain drive is less than or equal to 5°, and the center distance of the multi-wedge belt is recommended to choose 73.7mm.
Selection of installation mode:
There are various installation methods for roller, such as spring pressing type, internal thread, external thread, flat tenon, semicircular flat (D type), pin hole, etc. Among them, the internal thread is the most commonly used, followed by spring pressing, and the other ways are used on specific occasions, which are not commonly used.
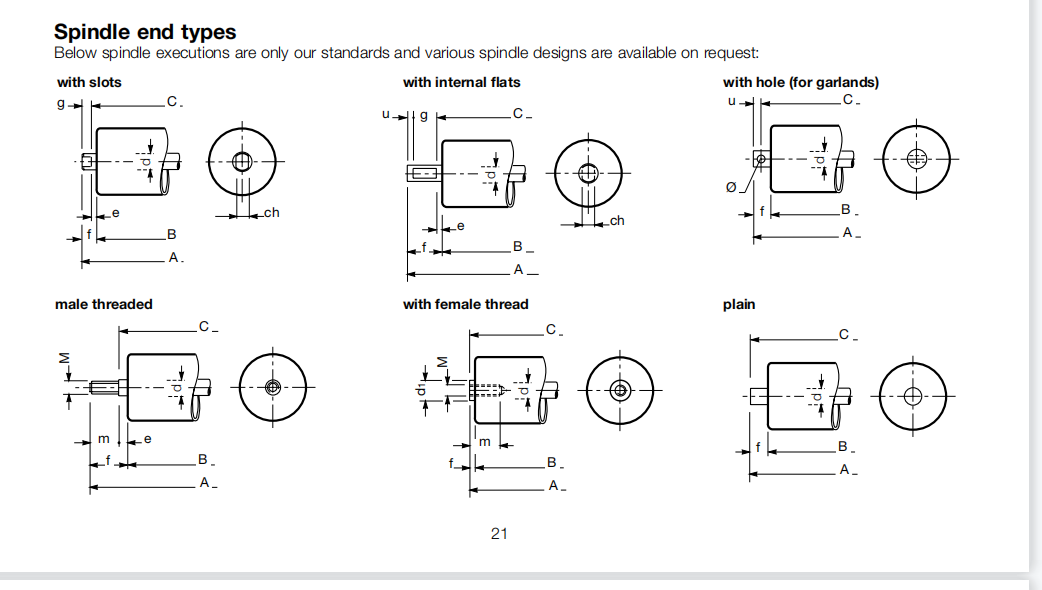
Comparison of commonly used mounting methods.
1) Spring press-in type.
a. The most commonly used mounting method in non-powered rollers, is very easy and fast to install and dismantle.
b. A certain installation margin is required between the inner width of the frame and the roller, which will vary according to the diameter, aperture, and height, usually leaving a gap of 0.5 to 1mm on one side.
c. Additional ties are required between the frames to stabilize and reinforce the frame.
d. It is not recommended that the sprocket roller be mounted with a loose connection such as a spring press-in type.
2) Internal thread.
a. It is the most commonly used mounting method in powered conveyors such as sprocket rollers, where the rollers and the frame are connected as a single unit by means of bolts at both ends.
b. It is relatively time-consuming to install and dismantle the roller.
c. The hole in the frame should not be too large to reduce the height difference of the roller after installation (the gap is generally 0.5mm, for example, for M8, it is recommended that the hole in the frame should be Φ8.5mm).
d. When the frame is made of aluminum profile, it is recommended to choose the configuration of "large shaft diameter and small thread" to prevent the shaft from penetrating the aluminum profile after locking.
3) Flat tenons.
a. Derived from mine slotted roller sets, where the round shaft core end is milled flat on both sides and snapped into the corresponding frame slot, making installation and removal extremely easy.
b. Lack of upward directional restraint, so mostly used as belt machine rollers, not suitable for power conveyance such as sprockets and multi-chamber belts.
Regarding load and load carry.
Load: This is the maximum load that can be carried on a roller that can be driven into operation. The load is influenced not only by the load carried by a single roller, but also by the installation form of the roller, the drive arrangement, and the drive capacity of the drive components. In power transmission, the load plays a decisive role.
Load bearing: This is the maximum load that a roller can carry. The main factors influencing load carrying are: the cylinder, the shaft, and the bearings, and are determined by the weakest of them all. In general, increasing the wall thickness only increases the impact resistance of the cylinder and does not have a significant effect on the load carrying capacity.
GCS reserves the right to change dimensions and critical data at any time without any notice. Customers must ensure that they receive certified drawings from GCS prior to finalizing design details.
Post time: Jul-05-2022